
With Premium centrifugal process ensures cast dense components, which ensures refined grain size which increase mechanical properties by 20% which translates to your reduced tooling cost by 15%-20% and rest assured, quality assured at every step.
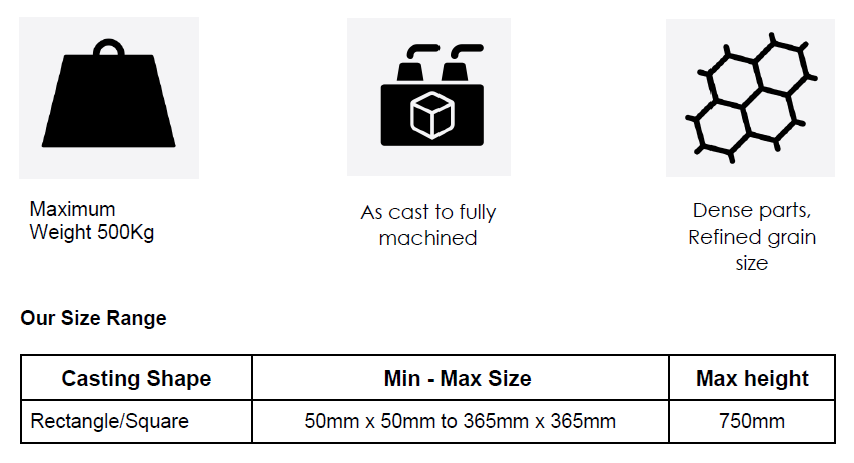
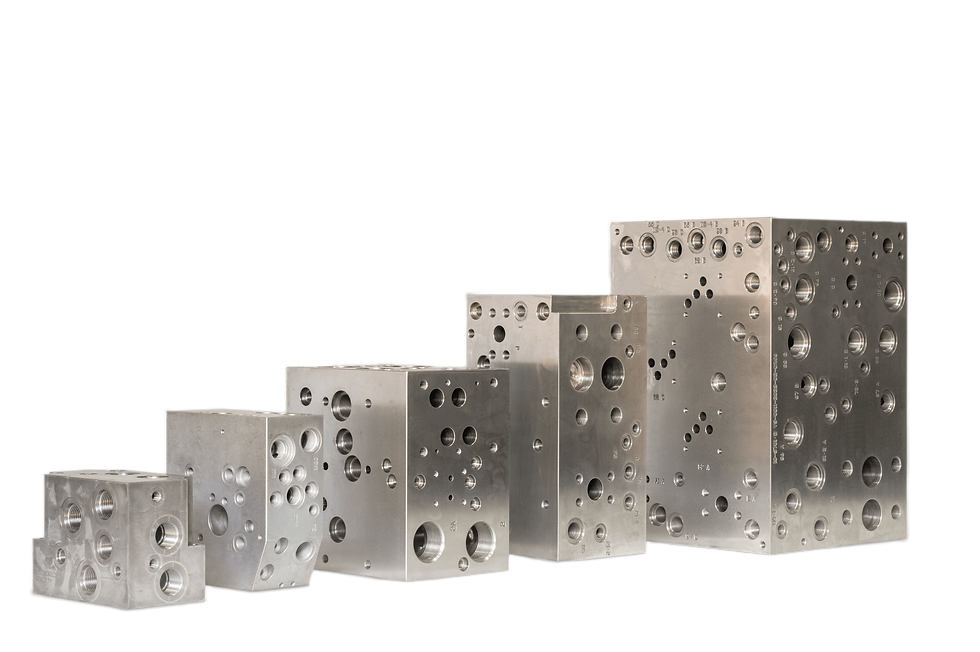
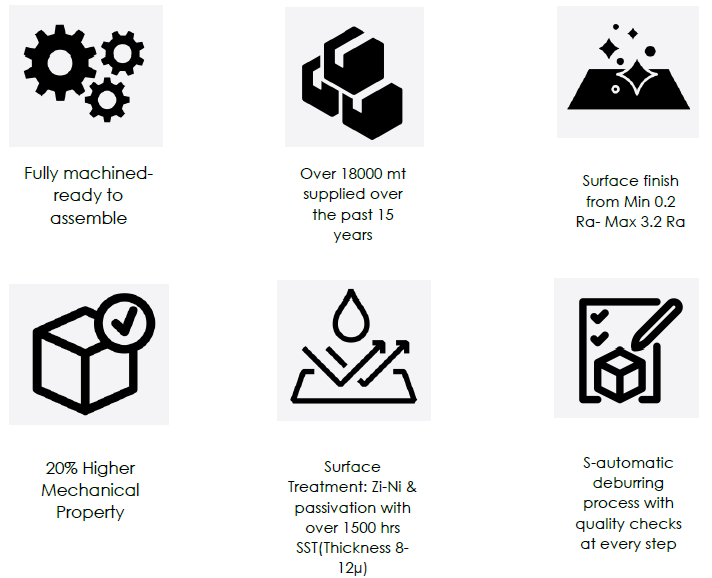
Your Hydraulic Component Machining Experts
Dimensional Accuracy

Hydraulic components must adhere to strict dimensional tolerances to ensure proper fit, assembly, and operation within hydraulic systems. Any deviations can lead to leaks, inefficiencies, or even system failures. Hence the stringent controls, shorter inspection frequency and laborious testing quality plans are inherent part of VSPL machining process.
Surface Finish
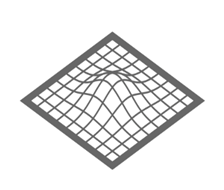
Smooth and consistent surface finishes are crucial to prevent friction and wear between components. Inadequate surface finish can lead to increased friction, decreased performance, and a shorter component lifespan. Hence tools and parameters are optimised and monitored during production to ensure surface finish criticality. At VSPL, an integrated approach of metallurgy and machining process ensures needed enhanced surface properties.
Sealing integrity
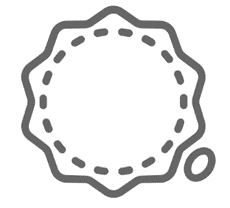
Having exposure to hydraulic components extensively, we understand the component design and its functional needs. Proper seals and gaskets are essential to prevent fluid leakage and maintain system integrity. Accurate machining and assembly are required to achieve reliable sealing, minimizing the risk of hydraulic fluid leakage. These part requirements are translated into the quality and machining process.
Tight Tolerances

Misalignment between assemblies can lead to uneven pressure distribution and decreased system efficiency. Hydraulic components, especially those in manifolds and assemblies, must be machined with precision to maintain angular and parallel. We adapt to special machines and processes ensures perpendicular and parallel tolerances.
Angular and parallel Alignment

In components like manifolds, accurately machined cavities and passages are essential for fluid flow. Any irregularities or misalignments can lead to flow disruptions and inefficiencies. Special tooling and machining processes are adapted to machine and test cavity consistency and regularities.
Cavities and Passages

Hydraulic systems are sensitive to contamination, so components must be machined, deburring and handled in a clean environment to avoid introducing particles that could damage the system or clog passages. Particular to machining hydraulic components, deburring is a critical operation. Burrs left in the system has catastrophic effects to the hydraulic system. At VSPL, we understand the significance of a burr free part which is clean and meets the highest standard of particle size and volumetric cleanliness levels.
Deburring and Cleanliness

Hydraulic systems operate under high pressures, and even minor deviations from specified tolerances can have significant impacts on performance. Tolerances from blue prints are further reduced and machined to tight tolerances to ensure proper functionality and prevent leakage.
コメント