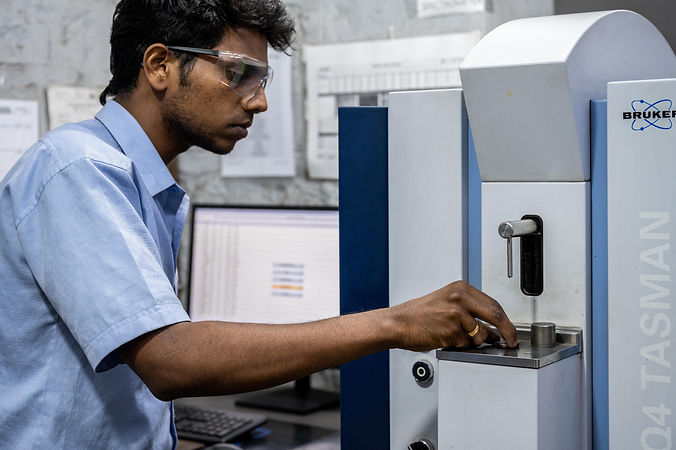
In Pursuit of Perfection
Our Commitment to Quality Assurance
Our material manufacturing prowess lies in our Process Control Capabilities, reflecting an unparalleled dedication to product quality and assurance.
Casting Quality
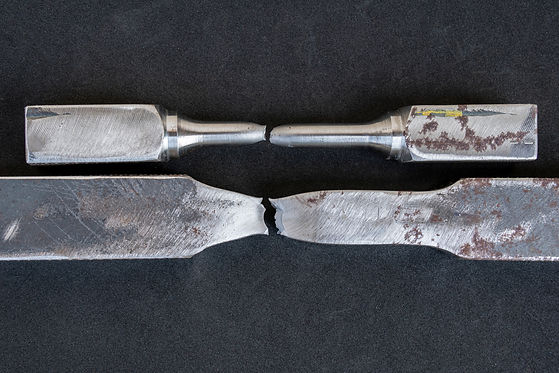
Material Engineering Redefined - Mechanical Testing
In mechanical testing, we take pride in achieving mechanical properties on cast parts - Not separate test samples. This approach ensures that the mechanical properties we measure are a true reflection of the final cast part's performance. This is particularly true for our centrifugally cast parts.
For Rapid Prototypes and Conventional cast parts, our testing procedures match standards or specific demands. Use this to Value Engineering your components using centrifugally cast parts, and optimise design safety factors - presenting opportunities to curtail lifetime expenses. For in-depth metallurgical opportunities, contact our experts - Contact Us.
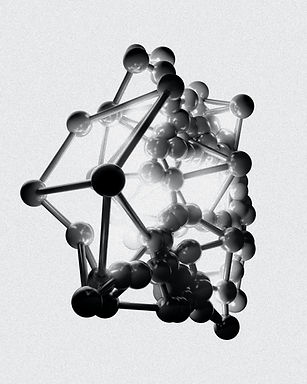
Chemistry Assurance and Certification.
When you work with us you will soon realise, quality at VSPL is a culture and core values. Our dedication to assurance is evident in our internal testing processes. Each heat we produce undergoes rigorous mechanical property testing, while every bath is meticulously checked for its chemical composition. Our commitment to producing outstanding results is reflected in our 3.1 and 3.2 test certificates, ensuring that every single batch meets the highest standards.
Quality Assurance and NDT
Exceptional Quality for every part, how it is achieved
Quality is the foundation of everything we do. That's why every part we produce undergoes 100% ultrasonic testing. This rigorous process is a testament to our confidence in our manufacturing consistency and processes. Our team, comprised of NDT qualified engineers, brings years of experience to the table. They are adept at part testing and identification, ensuring that each component meets our high standards. Our capabilities include Dye Penetrant Testing for detection of surface defects and Magnetic Particle Inspection (MPI) further underscores detecting even the slightest stress-induced deformations, leaving no room for compromise.
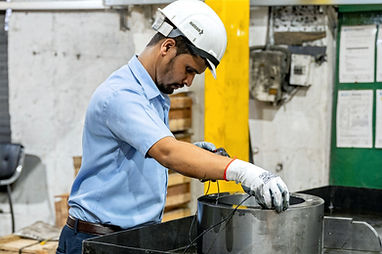
Centrifugally cast-parts Proof Machined - Ensure Quality of testing
Level 1 - 100% Ultrasonic Testing
Magnetic Particle Inspection

Machining Quality
Why we are your best Machining Partners
Quality at every step
BluePrint to Brilliance: Nurturing Quality every step - APQP
Our approach towards quality is with meticulous Planning. Our advanced quality product planning process lays the foundation for every project. From design to production, we adhere to a comprehensive roadmap that defines every step of the journey. This approach not only ensures efficiency but also guarantees that each product meets the highest quality standards.
Expertise, Experience - Risk Identification and Mitigation
Quality is about preventing issues before they arise. Focus is on establishing a robust manufacturing process and delivers high quality products. We rely on our combination of experience, expertise and development process to proactively identify and mitigate risks at every stage of production. Our rigorous risk assessment procedures allow us to address potential challenges before they impact the final product, enabling us to deliver high quality products every time.
Automation for Precision and Consistency
Our reliance and investment on Automation is key towards our quality process. We utilize on-machine probes for precise offset measurements of both workpieces and tools. By continuously monitoring tool life and load measurements, we maintain a real-time overview of the machining process. This not only guarantees quality assurance but also enhances overall efficiency. Know More
Comprehensive Traceability
Traceability is crucial for quality control. We implement a comprehensive traceability system that allows us to track each component's journey from raw material to finished product. Unique heat code is generated for every product to identify the bath and a unique ID, in collaboration with the customer is generated for every part. This transparency ensures accountability and quality throughout the process.
Customer Collaboration and Feedback
We consider our clients as partners in quality. Collaboration and open communication with clients enable us to align our processes with their unique needs and expectations. Client feedback is invaluable in our journey towards constant enhancement and consistent product quality.